Uplift Rebuild Part 2 – New wheels
8th March 2024
An issue I ran into during the initial build of Uplift back in 2017 was how to hold the wheels onto the gearbox shafts in a durable enough way that it would survive in combat.
The wheels I was using were 80mm diameter nylon castor hubs with offcuts of bike tread screwed round them. Many robots do something similar to this as it’s a great way to make relatively cheap but durable and grippy wheels:
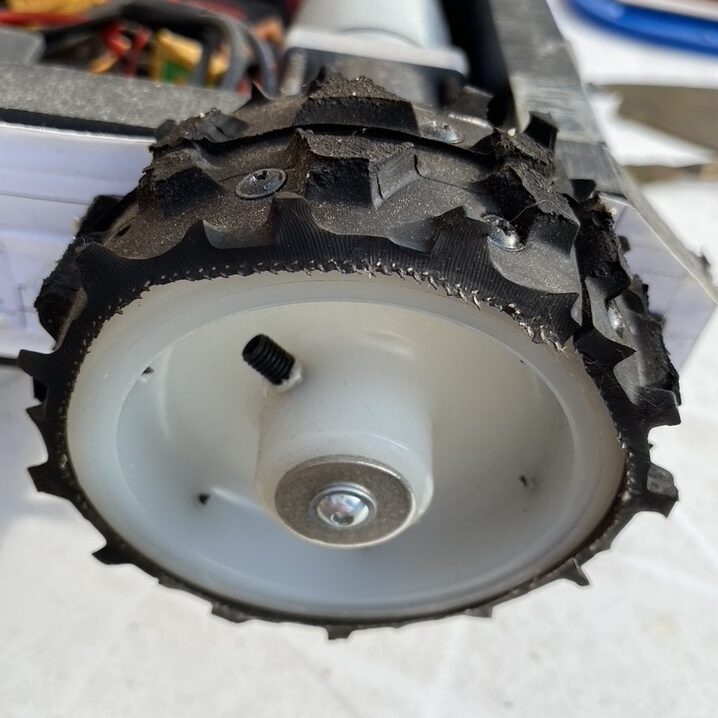
To hold them onto the gearbox shaft, I simply drilled an undersized hole in the centre hub and screwed a setscrew in until it gripped onto the flat part of the shaft that forms the keyway.
Now Nylon holds a thread quite well and for driving around the road or bouncing down the small steps on my patio this approach worked fine, however I had some serious concerns about it’s durability in a fight.
I knew the best approach would be to cut keyways into the Nylon hubs that matched the gearbox shaft keyway, removing the need for any delicate set screws. The problem was I didn’t (and actually as of 2024 still don’t) own any sort of press or a keyway broaching set, so cutting my own keyways was not really an option.
Fast forward to 2024 though and Ranglebox now sell wheels with pre-cut keyways, in the right diameter and the right bore size to fit the gearbox shafts. I bought some keysteel, cut it down to length with a hacksaw and after some filing got it to press snugly into the keyways on the gearbox shafts by clamping them together with a G-clamp:
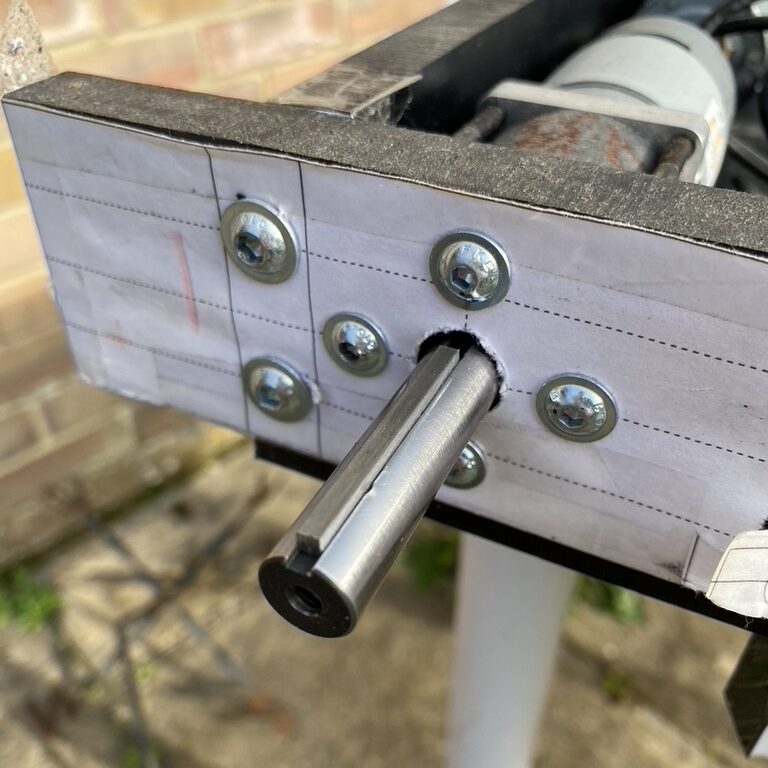
(Note the damage to the shaft caused by the set screw slipping – another reason to move away from set screws!)
Problem solved!
Well, almost. You see, while Uplift does use Ranglebox gearboxes (which these wheels are designed to fit perfectly), it actually uses the original models from 2016/2017. These older ones have a 3mm keyway whereas the newer versions use 4mm, meaning the keyway on the wheels was ever so slightly too large:
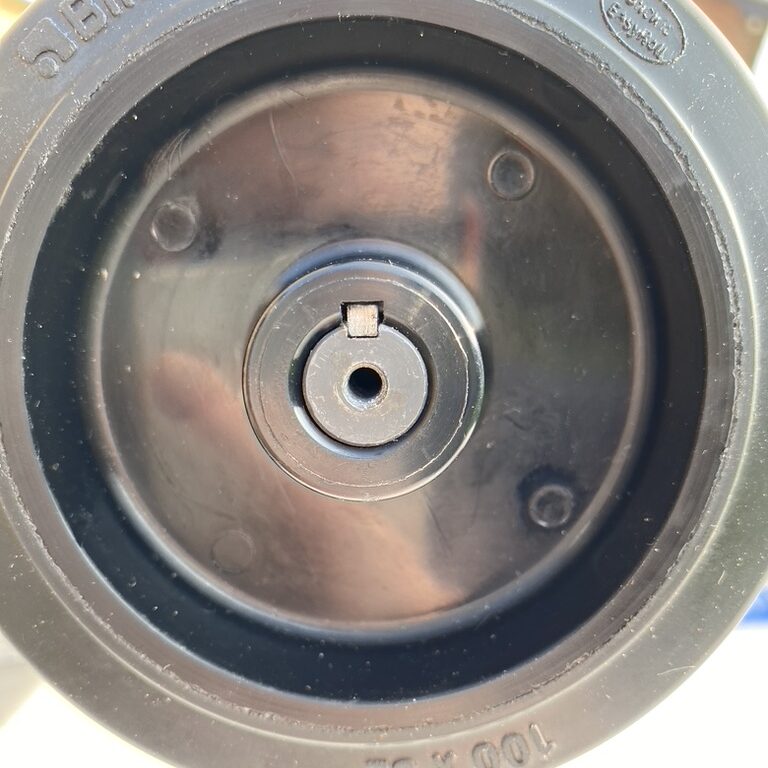
The wheels fitted and couldn’t freely rotate very much without also turning the gearbox which was good, but they were definitely a little loose and that amount of movement would likely start to damage the plastic hubs after continued use.
Enter 3D printing! I decided to try printing some shims to fill the gap. Essentially a little plastic sleeve that would slide over the 3mm key and “convert” the top half from 3mm to 4mm.
I made some to test and they worked perfectly, creating a snug fit between the wheel hub and the gearbox shaft and eliminating any slop between the movement of the wheel and the gearbox turning.
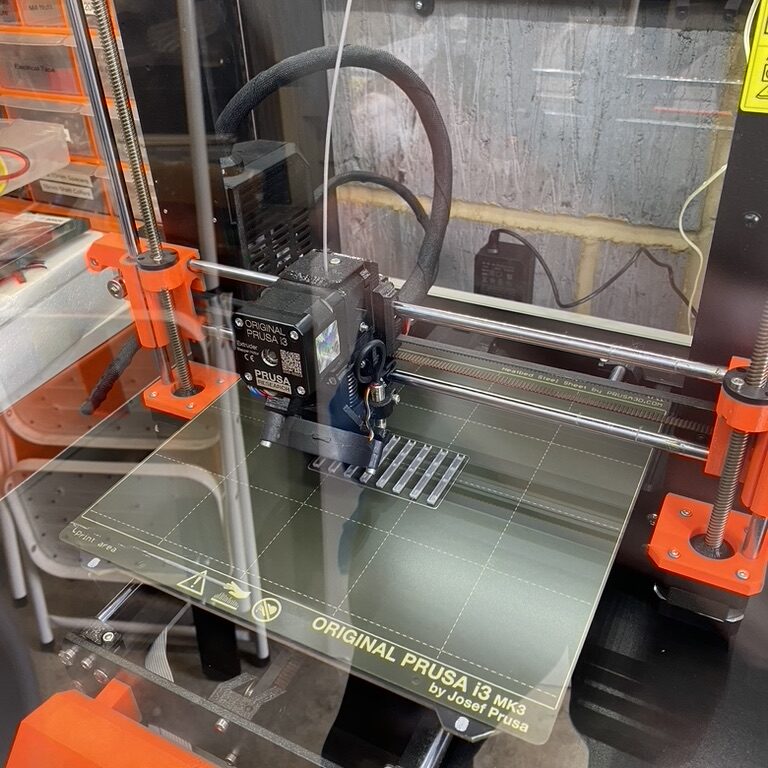
I’m not sure how durable these shims will turn out to be, especially as they are only very thin PLA, however my theory is that because they will be completely sealed between the wheel, the robot and the end washer holding the wheel on, even if they do break the bits will have nowhere to go. So providing we give them a quick check over after each fight, it should be fine?
In any case, here’s Uplift sporting it’s shiny new wheels:
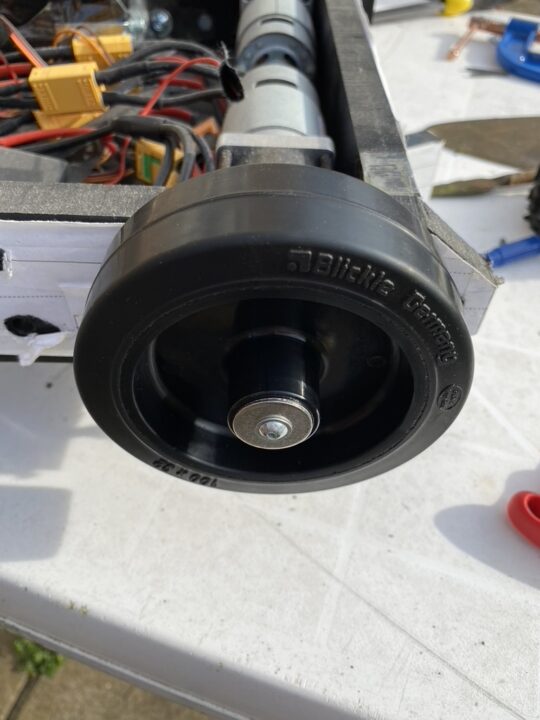
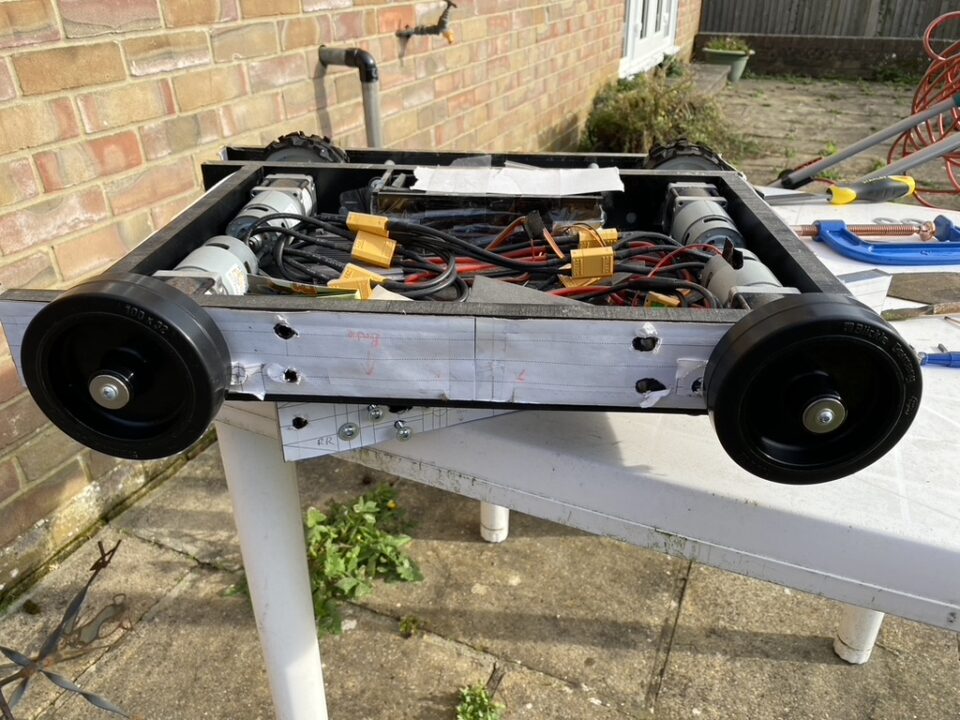