Uplift Rebuild Part 6 – Lifter motor and gearing
25th May 2024
Uplift’s lifting arm will be driven by a cordless drill “500 size” brushed motor, connected to a 132:1 P60 planetary gearbox from Banebots. The output shaft of the gearbox will have a 14 tooth steel spur gear, which will mesh with a 40 tooth spur gear on the main lifting arm axle (made from a 16mm shoulder bolt).
Hopefully, this will provide enough power to lift a 13.6kg opponent without any issues. I’m not looking to flip other robots clean into the air, just turning them over in a (relatively) controlled fashion is the goal here.
Before I could mate the motor to the gearbox, I needed to shorten the motor’s output shaft by a few millimetres so that it would fit snugly against the gearbox face. A couple of minutes with a Dremel grinding disc did the trick (unmodified spare motor on the left for comparison):
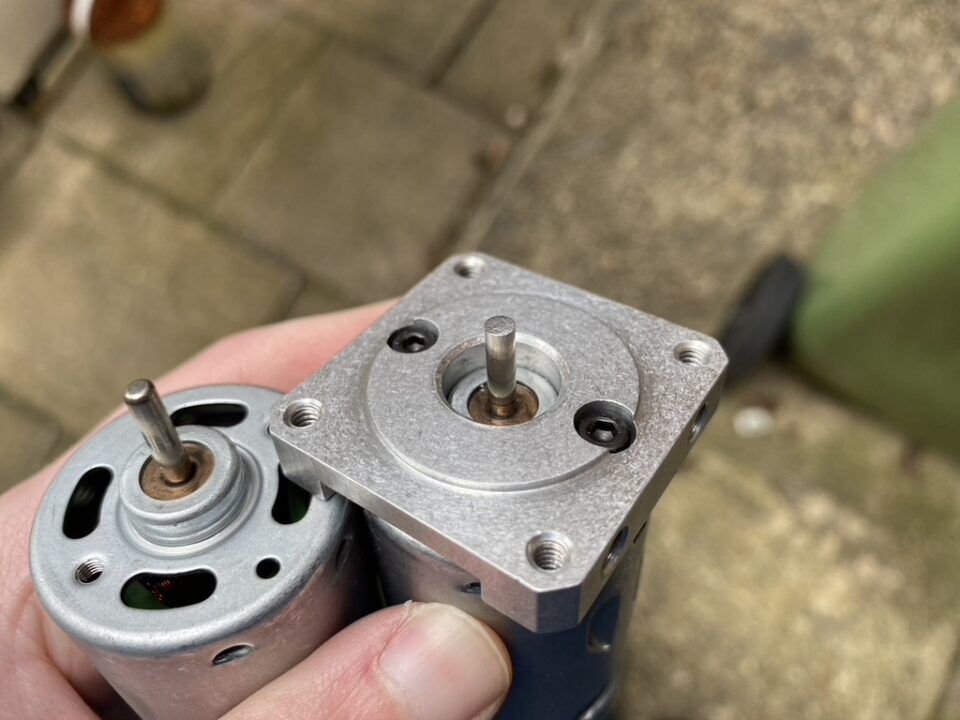
Now I could press fit the pinion gear to the motor shaft. This was a bit tricky as I don’t own a press but I found squeezing them together in a bench vice worked well, being careful not to bend the motor shaft in the process:
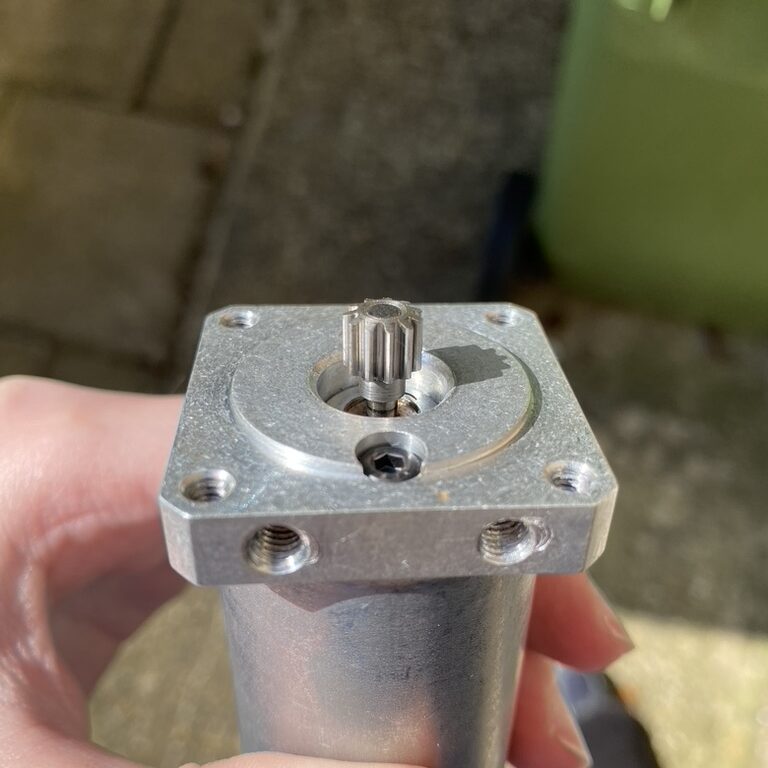
I soldered some wires onto the motor and hooked it up to my bench power supply to check everything rotated smoothly – which it did!
Here’s the full lifter assembly now mounted in the robot. As you can see, it’s a pretty tight fit with the wires on the lifter motor almost getting squashed against the frame:
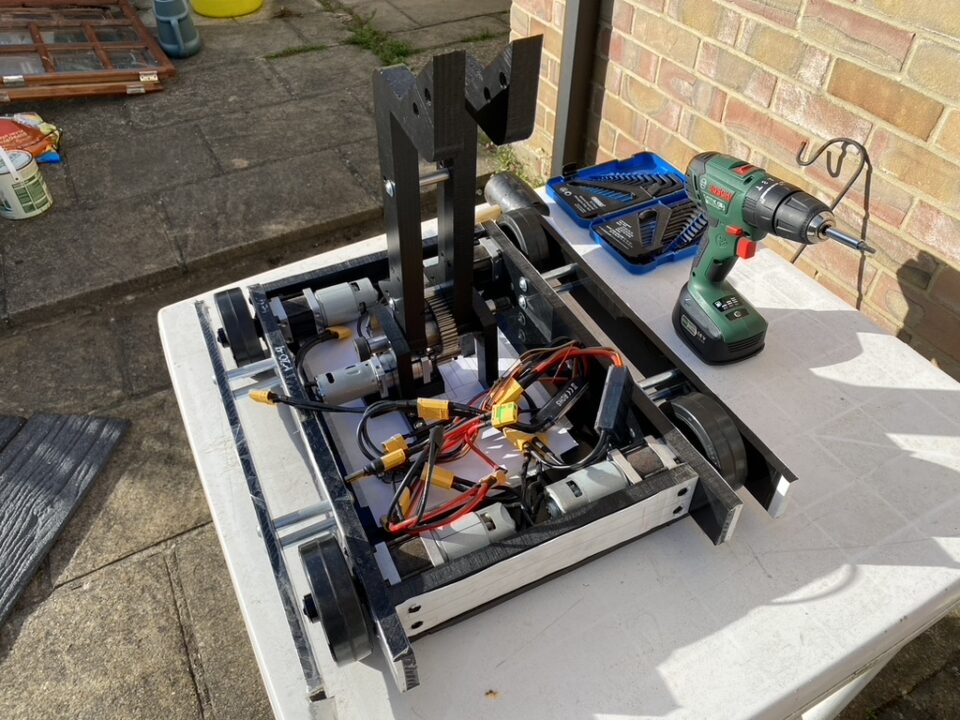
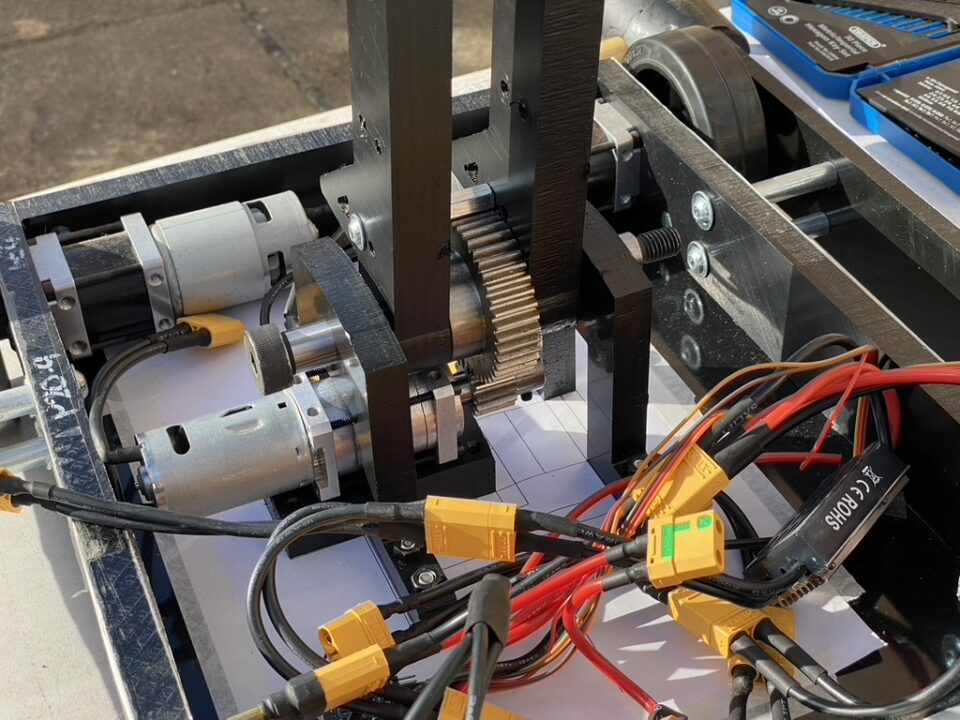
In the second picture you can see the hex spacer that squeezes into the teeth of the spur gear and locks the lifting arm in place so that when gear turns, the arm moves up or down.
Overall, I’m pleased with how this is turning out. Uplift is finally starting to look like a proper combat robot!
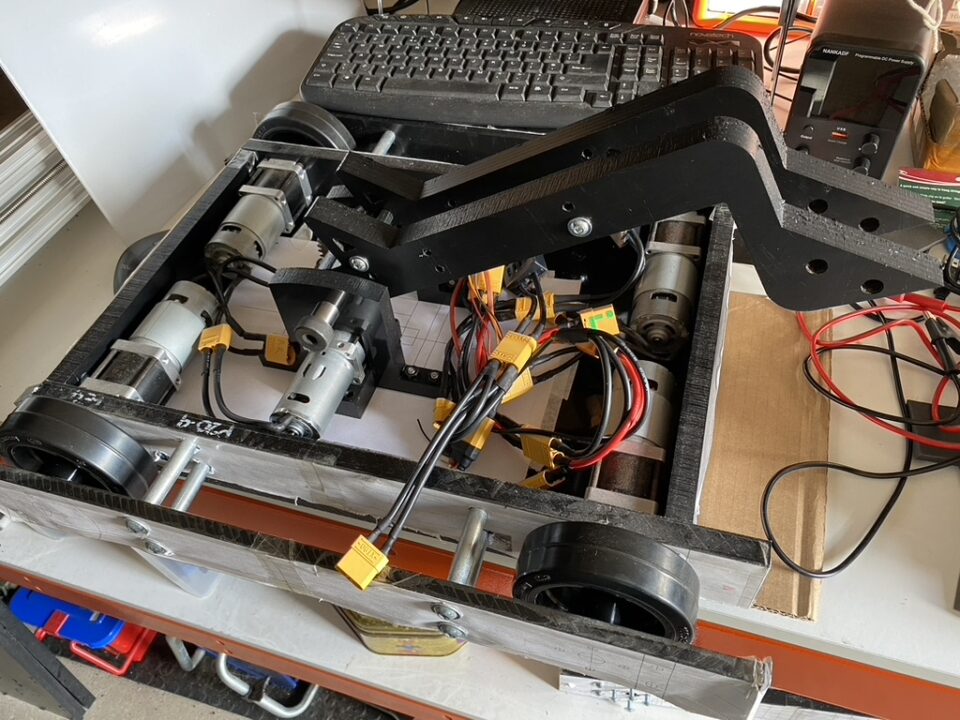
With the main lifter elements sorted, I can now turn my attention to finishing the armour and making some nice to have extras such as hinged front forks to help get underneath opponents.